Plastic extrusion for reinforced, durable materials
Plastic extrusion for reinforced, durable materials
Blog Article
A Comprehensive Guide to the Process and Advantages of Plastic Extrusion
In the vast realm of manufacturing, plastic extrusion emerges as a necessary and very efficient process. Translating raw plastic into constant accounts, it caters to a wide variety of industries with its impressive adaptability.
Comprehending the Fundamentals of Plastic Extrusion
While it might show up complicated at first glimpse, the process of plastic extrusion is essentially basic. The process starts with the feeding of plastic product, in the kind of granules, powders, or pellets, right into a warmed barrel. The designed plastic is after that cooled down, solidified, and reduced into preferred sizes, completing the procedure.
The Technical Refine of Plastic Extrusion Explained
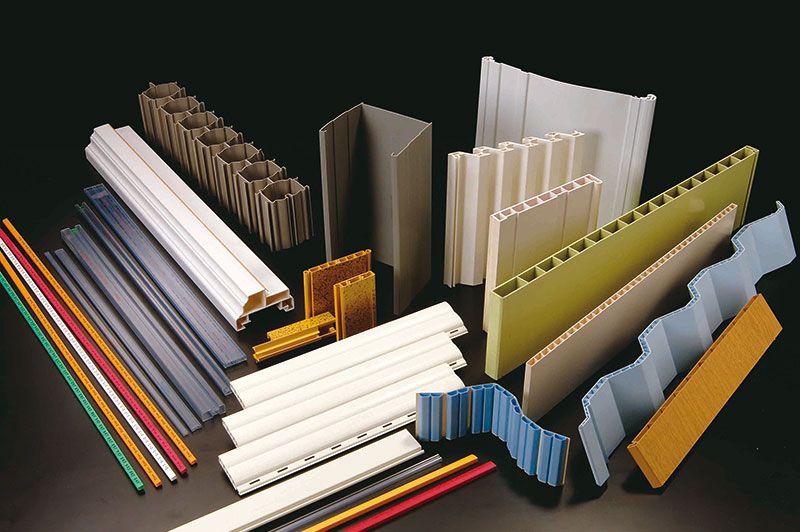
Types of Plastic Suitable for Extrusion
The selection of the best kind of plastic is an important element of the extrusion procedure. Numerous plastics offer distinct residential or commercial properties, making them a lot more suited to particular applications. Polyethylene, for example, is typically used due to its low cost and very easy formability. It offers outstanding resistance to chemicals and moisture, making it suitable for items like tubing and containers. In a similar way, polypropylene is another prominent option due to its high melting factor and resistance to exhaustion. For more robust applications, polystyrene and PVC (polyvinyl chloride) are commonly picked for their toughness and longevity. These are usual alternatives, the selection ultimately depends on the certain needs of the product being generated. So, recognizing these plastic kinds can substantially improve the extrusion process.
Contrasting Plastic Extrusion to Various Other Plastic Forming Approaches
Understanding the types of plastic ideal for extrusion leads the way for a broader discussion on how plastic extrusion compares to various other plastic forming techniques. These include injection molding, impact molding, and thermoforming. Each approach has its special usages and benefits. Injection molding, for example, is outstanding for producing elaborate components, while strike molding is ideal for hollow objects like bottles. Thermoforming excels at forming large or superficial parts. Plastic extrusion is unequaled when it comes to producing continuous profiles, such as pipelines, gaskets, and seals. It additionally permits a consistent cross-section along the size of the item. Thus, the selection of technique mainly depends on the end-product requirements and requirements.
Key Advantages of Plastic Extrusion in Production
In the realm of production, plastic extrusion uses many substantial advantages. One remarkable advantage is the cost-effectiveness of the process, which makes it a financially attractive production technique. Additionally, this technique gives exceptional product flexibility and enhanced manufacturing rate, therefore raising general manufacturing performance.
Economical Manufacturing Technique
Plastic extrusion jumps to the center as an economical production method in manufacturing. This process stands apart for its capability to produce high quantities of material rapidly and successfully, offering producers with substantial financial savings. The key expense benefit is the capacity to make use of much less costly resources. Extrusion uses polycarbonate materials, which are much less pricey compared to steels or porcelains. Additionally, the extrusion procedure itself is relatively simple, lowering labor expenses. Additionally, plastic extrusion requires much less power than traditional manufacturing browse around these guys techniques, adding to reduced operational expenses. The procedure additionally decreases waste, as any type of excess or malfunctioning products can be reused and reused, giving another layer of cost-effectiveness. On the whole, the monetary benefits make plastic extrusion a very attractive choice in the manufacturing industry.
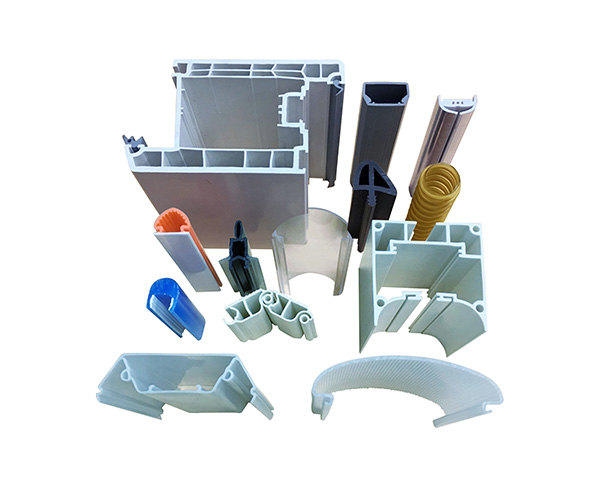
Superior Item Flexibility
Past the cost-effectiveness of plastic extrusion, an additional significant advantage in producing lies in its remarkable product adaptability. This makes plastic extrusion a suitable solution for industries that require tailored plastic parts, such as automobile, construction, and packaging. In essence, plastic extrusion's item versatility cultivates advancement while boosting operational performance.
Enhanced Production Speed
A substantial benefit of plastic extrusion lies in its improved production rate. Few various other production procedures can match the speed of plastic extrusion. In addition, the capacity to preserve constant high-speed manufacturing without giving up item top quality establishes plastic extrusion apart from other techniques.
Real-world Applications and Impacts of Plastic Extrusion
In the world of production, the method of plastic extrusion holds profound importance. The economic benefit of plastic extrusion, primarily its cost-effective and high-volume result, has actually transformed manufacturing. The industry is persistently striving for developments in recyclable and naturally degradable products, indicating a future where the benefits of plastic extrusion can be kept without compromising environmental sustainability.
Conclusion
Finally, plastic extrusion is a very reliable and reliable method of changing resources into diverse products. It uses countless advantages over various other plastic creating approaches, consisting of cost-effectiveness, high outcome, minimal waste, and design adaptability. Its effect is profoundly really felt in different industries such as construction, automotive, and durable goods, making it a crucial process in today's production landscape.
Digging deeper into the technological process of plastic extrusion, it starts with the choice of the appropriate plastic product. As soon as cooled down, the plastic is reduced right into the needed lengths or wound onto reels if the item is a resource plastic movie or sheet - plastic extrusion. Comparing Plastic Extrusion to Various Other Plastic Forming Techniques
Understanding the kinds of plastic suitable for extrusion leads the method for a broader conversation on just how plastic extrusion stacks up against other plastic developing methods. Few other manufacturing procedures can match the rate of next plastic extrusion.
Report this page